 Книжкові видання та компакт-диски  Журнали та продовжувані видання  Автореферати дисертацій  Реферативна база даних  Наукова періодика України  Тематичний навігатор  Авторитетний файл імен осіб
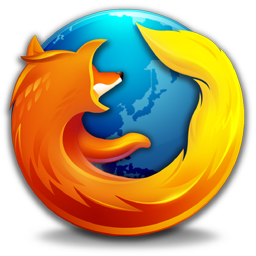 |
Для швидкої роботи та реалізації всіх функціональних можливостей пошукової системи використовуйте браузер "Mozilla Firefox" |
|
|
Повнотекстовий пошук
Пошуковий запит: (<.>AT=Kalchenko Building a model of$<.>) |
Загальна кількість знайдених документів : 2
Представлено документи з 1 до 2
|
1. |
Kalchenko V. Building a model of dressing the working surfaces of wheels during the two-side grinding of round end faces at CNC machines [Електронний ресурс] / V. Kalchenko, V. Kalchenko, A. Kolohoida, A. Yeroshenko, D. Kalchenko // Eastern-European journal of enterprise technologies. - 2022. - № 1(1). - С. 86-93. - Режим доступу: http://nbuv.gov.ua/UJRN/Vejpte_2022_1(1)__12 This paper reports the spatial mathematical modeling of the process of dressing the working surface of grinding wheels for implementing the double-sided grinding of the ends of cylindrical components. Parts with high-precision end surfaces that are commonly used include bearing rollers, piston fingers, crosspieces of cardan shafts, and others. The geometric accuracy of surfaces is ensured by simultaneously grinding the ends at two-sided end-grinding machines with crossed axes of the part and wheels that operate under a self-blunting mode. Before starting the machining, the wheels are dressed in a working position. Moreover, the total orientation angle of the tools is selected subject to the condition of uniform distribution of allowance along the rough sections of wheels. Dressing involves a single-crystal diamond tool with a variable feed. That ensures different development of the surface of abrasive tools, which prolongs their operating time between dressings and improves overall stability. The constant size of micro irregularities at the calibration site enhances the quality of machining. The calibration site is made in the form of a straight line belonging to the plane that passes through the axis of rotation of the wheel and is perpendicular to the plane of the machined part. Based on the spatial mathematical models of the processes of removal of allowance and shape formation when dressing the wheel, the surface of the grinding wheel was investigated. Mathematical models for shaping the ends of parts when grinding with wheels with conical calibration sites have been proposed; it is shown that when applying the proposed machining scheme, there is no geometric error in the size of the part. In addition, due to the uniform distribution of the allowance along the rough area of the wheel, the quality of the surface layer of the ends of parts increases. The devised method for dressing the working surface of wheels could be used to grind the ends of non-circular components.This paper reports the spatial modeling of the dressing process of grinding wheels with a conical calibration area to enable two-sided end grinding of cylindrical parts. Components with cylindrical end surfaces are common in the industry, for example, bearing rollers, crosses, piston fingers, and others. High requirements are put forward for the accuracy and quality of the end surfaces. The most efficient is to machine them simultaneously on a double-sided face grinding machine. To improve the quality, grinding is carried out by oriented wheels. The wheel's angle of rotation in the vertical plane is chosen subject to the uniform distribution of the allowance along a working surface; this makes it possible to reduce the temperature in the cutting zone and improve machining conditions. To improve the accuracy, grinding wheels are provided with a conical calibration area whose rectilinear generatrix is in the plane passing through the axis of wheel rotation and is perpendicular to the end of the part. The minimum permissible length of the calibration area depends on the diameter of the parts being machined; that makes it possible to utilize the work surface more efficiently. Two wheels are dressed simultaneously using diamond pencils that are symmetrically installed in a part feed drum. The angular velocity when dressing the rough area of the wheel is constant, which ensures its different development, and it gradually decreases when dressing the calibration area to provide for its constant roughness. In general, this prolongs the resource of grinding wheels and the quality of machining. The wheels are given axial movement to ensure the straightness of the cone calibration area. The dressing technique reported here can be used on machines equipped with a numerical software control system and without it. It could also be applied in the machining of parts with non-round ends.
| 2. |
Kalchenko V. Building a model of the process of shaping tapered calibrating areas of wheels at the two-sided grinding of round ends [Електронний ресурс] / V. Kalchenko, V. Kalchenko, A. Kolohoida, O. Kalchenko, D. Kalchenko // Eastern-European journal of enterprise technologies. - 2022. - № 2(1). - С. 62-70. - Режим доступу: http://nbuv.gov.ua/UJRN/Vejpte_2022_2(1)__9 This paper reports the spatial mathematical modeling of the process of dressing the working surface of grinding wheels for implementing the double-sided grinding of the ends of cylindrical components. Parts with high-precision end surfaces that are commonly used include bearing rollers, piston fingers, crosspieces of cardan shafts, and others. The geometric accuracy of surfaces is ensured by simultaneously grinding the ends at two-sided end-grinding machines with crossed axes of the part and wheels that operate under a self-blunting mode. Before starting the machining, the wheels are dressed in a working position. Moreover, the total orientation angle of the tools is selected subject to the condition of uniform distribution of allowance along the rough sections of wheels. Dressing involves a single-crystal diamond tool with a variable feed. That ensures different development of the surface of abrasive tools, which prolongs their operating time between dressings and improves overall stability. The constant size of micro irregularities at the calibration site enhances the quality of machining. The calibration site is made in the form of a straight line belonging to the plane that passes through the axis of rotation of the wheel and is perpendicular to the plane of the machined part. Based on the spatial mathematical models of the processes of removal of allowance and shape formation when dressing the wheel, the surface of the grinding wheel was investigated. Mathematical models for shaping the ends of parts when grinding with wheels with conical calibration sites have been proposed; it is shown that when applying the proposed machining scheme, there is no geometric error in the size of the part. In addition, due to the uniform distribution of the allowance along the rough area of the wheel, the quality of the surface layer of the ends of parts increases. The devised method for dressing the working surface of wheels could be used to grind the ends of non-circular components.This paper reports the spatial modeling of the dressing process of grinding wheels with a conical calibration area to enable two-sided end grinding of cylindrical parts. Components with cylindrical end surfaces are common in the industry, for example, bearing rollers, crosses, piston fingers, and others. High requirements are put forward for the accuracy and quality of the end surfaces. The most efficient is to machine them simultaneously on a double-sided face grinding machine. To improve the quality, grinding is carried out by oriented wheels. The wheel's angle of rotation in the vertical plane is chosen subject to the uniform distribution of the allowance along a working surface; this makes it possible to reduce the temperature in the cutting zone and improve machining conditions. To improve the accuracy, grinding wheels are provided with a conical calibration area whose rectilinear generatrix is in the plane passing through the axis of wheel rotation and is perpendicular to the end of the part. The minimum permissible length of the calibration area depends on the diameter of the parts being machined; that makes it possible to utilize the work surface more efficiently. Two wheels are dressed simultaneously using diamond pencils that are symmetrically installed in a part feed drum. The angular velocity when dressing the rough area of the wheel is constant, which ensures its different development, and it gradually decreases when dressing the calibration area to provide for its constant roughness. In general, this prolongs the resource of grinding wheels and the quality of machining. The wheels are given axial movement to ensure the straightness of the cone calibration area. The dressing technique reported here can be used on machines equipped with a numerical software control system and without it. It could also be applied in the machining of parts with non-round ends.
|
|
|