 Віртуальна довідка  Тематичний інтернет-навігатор  Наукова електронна бібліотека  Автореферати дисертацій  Реферативна база даних  Книжкові видання та компакт-диски  Журнали та продовжувані видання
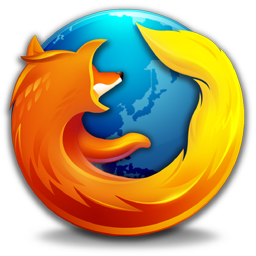 |
Для швидкої роботи та реалізації всіх функціональних можливостей пошукової системи використовуйте браузер "Mozilla Firefox" |
|
|
Формат представлення знайдених документів: | повний | стислий |
Пошуковий запит: (<.>I=Ж44086<.>) |
Загальна кількість знайдених документів : 181
Представлено документи з 1 до 20
|
| |
| | | | |
1. |
Bhagi L. K. Application of Taguchi method for optimization of continuous drive friction welding process parameters / L. K. Bhagi, Sh. Singh, I. Singh // Ukr. j. of mech. eng. and materials science. - 2016. - 2, № 1. - С. 1-10. - Бібліогр.: 10 назв. - англ.The objective of present study was to determine optimal conditions to achieve satisfactory friction welds between two dissimilar metals namely copper and carbon steel bars of same diameter. Three process parameters namely speed of rotation, axial pressure, and forge pressure were considered for the present study. Two multiple performance characteristics, considered were breaking load strength and upset. The optimization of the process parameters was done using ANOVA. The obtained results indicated that the most significant process parameters are axial pressure and rotational speed that affect the optimization of multiple performance characteristics. Індекс рубрикатора НБУВ: К641.712-1
Рубрики:
Шифр НБУВ: Ж44086 Пошук видання у каталогах НБУВ
|
| | | | |
2. |
Chovnyuk Yu. Dynamic modelling and control system of a single non-slender flexible robot's link rotating in a horizontal plane / Yu. Chovnyuk, Yu. Gumeniuk, M. Dikterjuk // Ukr. j. of mech. eng. and materials science. - 2016. - 2, № 1. - С. 11-30. - Бібліогр.: 14 назв. - англ.Most authors have ignored the effect of rotatory inertia and shear deformation. This practice is justified for slender flexible arms. According to the Timoshenko beam theory, the deflection due to shear force and rotatory inertia should be taken into account in modelling for high speed and high precision requirement when the ratio of the cross-sectional dimensions to length increases. Based on Hamilton's principle and Timoshenko's flexible beam theory, the dynamic model of a single non-slender flexible link is derived, and it is shown that the elastic motion is governed by a pair of coupled partial differential equations with coupled boundary conditions. Then the abstract form of the dynamic equations is studied, and the properties of the spectrum of the elastic operator appearing in the evolution equation are given. Furthermore, the eigenvalue problem of the elastic operator is solved in explicit form. The formulation and well-posedness of the state-space equation, as well as the transfer function of the dynamic control system of the non-slender flexible link, are studied by spectral analysis. Spectral analysis is used to study the well-posedness of the dynamic control system. The tracking control problem is studied and a feedback control scheme that controls the rigid-body motion and elastic behaviors simultaneously is derived based on a n-modal model. Closed-loop configuration of a control system, equivalent circuit of a dc-motor and the overall system block diagram are proposed. The stabilization of the closed-loop system is studied analytically. Finally, the tracking control problem is studied, a stabilizing feedback control law based on a n-modal model to suppress vibrations of the flexible link is derived, and the necessary and sufficient conditions that can guarantee the stability of the closed-loop system, are given. Simulation results are given as well. Індекс рубрикатора НБУВ: З813.11
Рубрики:
Шифр НБУВ: Ж44086 Пошук видання у каталогах НБУВ
|
| | | | |
3. |
Orgiyan A. Computation of shaping errors for fine boring of smooth and stepped holes / A. Orgiyan, A. Balanyuk, V. Kobelev, I. Tvorischuk // Ukr. j. of mech. eng. and materials science. - 2016. - 2, № 1. - С. 31-40. - Бібліогр.: 13 назв. - англ.On the basis of precision theory we propose the method of computation of static and dynamic errors of cross-sectional shapes of holes in fine boring of smooth and stepped holes. We consider particular cross-sectional shape errors caused by such factors: - Error of the tooled hole form caused by the axis hope displacement in the workpiece relative to the spindle axis; - Error of the tooled hole form caused by the hole out-of-roundness in the workpiece; - Error of the tooled hole form caused by unevenness of the cutter radial compliance at the angle of spindle rotation. According to time characteristics the errors can be divided into static with frequency substantially less than the lowest natural frequency of the process system, and dynamic, caused by vibrations. Static error rate is usually a multiple of the spindle speed. The computations of deviations from the roundness of the cross section caused by vibrations are determined by computing the amplitudes of forced vibrations. Computations of individual static errors based on the average values of compliance, the material being processed and the processing mode are reduced to construction of nomographs for various materials. Dynamic errors are determined by computation of forced vibrations amplitudes on the basis of systems of ordinary differential equations describing the vibrations of a machine closed dynamic system. These equations allow to compute the amplitude of the forced vibrations of smooth and stepped boring bars. A distinctive feature of the computations for multiple tooling is allowance for mutual influence of excitations arising at each step of a boring bar. It is assumed that at multiple tooling each of the working cutters creates its own errors, the values of which are found by the nomograms for single-cutter tooling. Full tooling error at each step caused by some source of error is determined as the sum of the errors: of both, own and additional, caused by all working cutters. Additional errors can be found through coefficients of influence through dividing by the respective cutter's own compliance and through multiplying by the appropriate factor of influence. We obtained results of computations and experiments of the dependence of the total error on the ratio of the boring bar steps lengths. Analysis of roundness charts of the bored holes shows that vibrations can be a factor largely determining the shape of the cross section of the hole. Experiments have shown that when the rotation speed changed the excitations of the spindle poles changed too. Under unfavorable excitation frequencies the tooling errors increase by 1,5 - 2 times. The study results allow us to compare the two most common ways to reduce the errors caused by elastic deformations: the use of the dynamic damper and the processing of holes in two runs. The experimental results confirm the non-monotonic dependence of the amplitudes of forced vibrations on the ratio of the boring bar steps lengths. Індекс рубрикатора НБУВ: К632.5-125
Рубрики:
Шифр НБУВ: Ж44086 Пошук видання у каталогах НБУВ
|
| | | | |
4. |
Koruniak P. Two-mass vibrating conveyer with nonparallel flat springs / P. Koruniak, I. Nishchenko, V. Shenbor, V. Korendiy // Ukr. j. of mech. eng. and materials science. - 2016. - 2, № 1. - С. 41-46. - Бібліогр.: 9 назв. - англ.The analysis of operation of vibrating conveyers with nonparallel placement of flat springs is carried out. The motion of mechanical oscillating system is investigated. The structure of the supporting unit for flat springs fastening is propounded. This structure allows simplifying of setting-up of two-mass vibrating conveyers with the aim to ensure the effective operation. The models of conveyers with nonparallel placement of springs, providing the accurate calculations of rigidities and angles of flat springs inclinations, considerably simplify the structures of conveyers and their setting-up to ensure the prescribed angles of vibrations. The proposed structure of fastening of flat springs ends allows increasing of operation efficiency of the two-mass vibrating conveyer. Due to such setting-up of the equipment it is possible to compensate some of its theoretical and structural faults. On the basis of presented investigations, it is planned to develop the three-mass models of conveyers-separators with transporting of separated components in different directions. Індекс рубрикатора НБУВ: О932.2
Рубрики:
Шифр НБУВ: Ж44086 Пошук видання у каталогах НБУВ
|
| | | | |
5. |
Dmyterko P. Research of influence of oscillations of tool-part system on roughness of surface layer during high-speed friction strengthening / P. Dmyterko, Yu. Novitskyi, V. Gurey // Ukr. j. of mech. eng. and materials science. - 2016. - 2, № 1. - С. 47-54. - Бібліогр.: 9 назв. - англ.During the discontinued friction strengthening except of the high-speed friction the processes of high-frequency shock loadings appears in the tool-part contact zone. The vibrations occur in the machine elastic system. During the vibrations of elastic systems, in the material of elastic elements and in the connecting units of the structure parts the energy dissipation into the ambient medium takes place. The energy dissipation of vibrations occurs due to the influence of the inelastic resistance forces on which the energy of the oscillatory system is spent. The vibrations of the tool-part system during the friction strengthening are similar to forced oscillations. However, for some particles of the part these oscillations are damped ones because the tool moves along the surface. The vibrations of the elastic system of the machine during the discontinued friction strengthening in the first approximation may be considered as free oscillations. For their investigation let us use the method of shock (impact) perturbation with a help of special measuring hammer which allows defining of the damping coefficient. With a help of the accelerometer and the hammer the shock (impact) curve and the registration curve of the tool-part vibrations were obtained. The obtained registration curve of tool-part vibrations was expanded into the Fourier series and with a help of MatLab program the obtained signal was filtered. Due to determination of the amplitude of vibrations and the oscillation period the logarithmic decrement of damping was defined. This parameter may be used for determination of the dynamic parameters of the oscillatory system of the converted machine. For defining the oscillations which arises in the part being machined we used the dynamometer, in which the piezo-crystal sensor was rigidly fixed. This sensor allows the readout of oscillations along three directions (along vertical, horizontal and transversal axis). Experimental research showed that the amplitude increased with increasing the number of processing modes and the oscillation character has exact wave-like form. The working process along the longitudinal direction has step-wise character. The single contact zone is heated to high temperatures; the metal softens; the friction coefficient decreases and the step-wise transportation of the part along the longitudal direction is being carried out. These phenomena are also confirmed by the figure of the machined surface and by the results of investigation of the topography of the machined surface. It is also experimentally determined that horizontal and vertical displacements of the spindle and the table vibrate with the frequencies close to resonance ones. With increasing of the tool rotation speed these vibrations have the character of damped ones and this phenomenon allows reducing the parameters of roughness, undulation and flatness of the surfaces being strengthened. Індекс рубрикатора НБУВ: К412.024 + Е63-125.4
Рубрики:
Шифр НБУВ: Ж44086 Пошук видання у каталогах НБУВ
|
| | | | |
6. |
Shenbor V. Analysis and improvement of two-mass vibrating tubular conveyers with two-cycle electromagnetic drive / V. Shenbor, P. Koruniak, V. Korendiy, V. Brusentsov, M. Brusentsova // Ukr. j. of mech. eng. and materials science. - 2016. - 2, № 1. - С. 55-64. - Бібліогр.: 13 назв. - англ.The analysis of structure diagrams of the two-mass tubular conveyer with two-cycle electromagnetic drive is carried out in the article. Two methods of designing of the elastic system are considered; calculation formulas for elastic system computation are deduced according to different requirements for the operating parameters of conveyers; the comparative analysis of two types of elastic systems is conducted. The recommendations for designing the lengthy tubular vibrating conveyers are presented. According to the considered structural diagrams of the elastic system the models of the lengthy vibrating conveyers with the transporting distances l = 1,5 - 4 m are developed. On the basis of these models the lengthy vibrotransporting systems with the transporting distance l = 5 - 30 m were developed, manufactured and applied in industry. The considered systems ensures the transportation of loose materials (porcelain composition, sand etc.) with maximal speeds up to 800 mm/sec and productivities (for tubes with internal diameter D = 100 mm) up to 30 tons per hour for. It is reasonable to use both considered schemes of elastic systems for development of vibrating tubular conveyers with electromagnetic drive. The conveyers may be designed in two modifications: overhead and supporting. The obtained dependencies allow optimization of the structure and considering the important technical parameters of conveyers (maximal permissible oscillations amplitude, springs stresses, productivity etc.) in the design phase. Індекс рубрикатора НБУВ: О932.2
Рубрики:
Шифр НБУВ: Ж44086 Пошук видання у каталогах НБУВ
|
| | | | |
7. |
Kozak A. Mathematical model of elements of automated system of loose materials dosing / A. Kozak // Ukr. j. of mech. eng. and materials science. - 2016. - 2, № 1. - С. 65-74. - Бібліогр.: 20 назв. - англ.Automatic dosing system for loose materials is widely used in construction, food and pharmaceutical industries to prepare various mixtures. The main criterion for optimization of such systems is the accuracy of dosing of each component of the mixture, which depends on the speed component dosing and other process factors. Technological requirements for product quality in production and the high cost of individual components of the mixture strictly regulate the developers of the automated system loose materials size dosing errors. Ensuring compliance with the maximumpossible mix recipe requires dosing of each component with high accuracy, which is a daunting task for engineers. Precision dispensing in automated systems is a function of the large number of systematic and random factors: size, shape and relative position of individual particles of the material; coupling coefficient of each other and of the structural elements of the dispenser; relative humidity of material dosage and indoor air; the height of the fall of the material in the receiving container; the value of the dispenser tilt to a level of horizon; electromechanical vibration and noise, etc. Developed simulation model of frequency-controlled electric screw feeder that is different from the known one facts that modeling of screw feeder is considering mass "falling pillar" which is constantly changing as the accumulation of material in the hopper. Індекс рубрикатора НБУВ: Л116.31
Рубрики:
Шифр НБУВ: Ж44086 Пошук видання у каталогах НБУВ
|
| | | | |
8. |
Maksimov S. Mag-welding of repair structures of main gas pipelines / S. Maksimov, O. Oleinik, A. Gavrilyuk // Ukr. j. of mech. eng. and materials science. - 2016. - 2, № 2. - С. 1-10. - Бібліогр.: 16 назв. - англ.Investigations on the development of a basic technology of the shielded-gas mechanized arc welding of strengthening structural elements which are used in repair of main gas pipelines were carried out. It is shown that the advanced welding wires Sv08G2S, Е71Т-1, DW-50, DW-A55 are in compliance with the requirements for providing the necessary level of mechanical characteristics, impact toughness of weld metal, content of diffusive hydrogen in the deposited metal and can be recommended for application in the further testing of technology for repair of the operating pipelines under the field conditions. The carried out works resulted in the working out of documentation on the technology of mechanized arc welding in shielding gases in repair of main gas pipelines of Ukraine. Індекс рубрикатора НБУВ: К641.510.023
Рубрики:
Шифр НБУВ: Ж44086 Пошук видання у каталогах НБУВ
|
| | | | |
9. |
Diveyev B. Sound transmission properties of composite layered structures in the lower frequency range / B. Diveyev // Ukr. j. of mech. eng. and materials science. - 2016. - 2, № 2. - С. 11-32. - Бібліогр.: 55 назв. - англ.This study aims to predict the sound transmission properties of composite layered plates structures in the lower frequency range. In present paper a novel procedure to derive the sound isolation parameters for layered plates is under discussion. This paper presents a new stress analysis method for the accurate determination of the detailed stress distributions in laminated plates subjected to cylindrical bending. Some approximate methods for the stress state predictions for laminated plates are presented here. The theoretical model described here incorporates deformations of each sheet of the lamina, which account for the effects of transverse shear deformation, transverse normal strain-stress and nonlinear variation of displacements with respect to the thickness coordinate. The main advantage of the present method is that it does not rely on strong assumptions about the model of the plate. Comparison with the Timoshenko beam theory is systematically made for analytical and approximation variants. The geometrical and mechanical parameters dependent frequency response functions and damping are presented for an arbitrary layered beam. The effective stiffness constants of equivalent to lamina Timoshenko beam (TB) and their damping properties have been determined by using a procedure based on multi-level numerical schemes and eigenfrequencies comparison. Numerical evaluations obtained for the vibration of the equivalent TB have been used to determine the sound transmission properties of laminated composite beams with the system of dynamic vibration absorbers (DVA's). The optimization of beams - DVA's system sound absorption properties is performed in the low frequency range. The results have shown that the presence of a DVA causes a decrease in the sound transmission in the low-frequency range. The extension of the present approach to various layered plates with various DVA's systems will be performed in order to obtain optimal sound insulation. Індекс рубрикатора НБУВ: Ж364.06
Рубрики:
Шифр НБУВ: Ж44086 Пошук видання у каталогах НБУВ
|
| | | | |
10. |
Trush V. Thermal processing of Zr-1 %Nb tube in oxygen- and nitrogen containing gaseous mediums / V. Trush, A. Luk'yanenko, V. Fedirko // Ukr. j. of mech. eng. and materials science. - 2016. - 2, № 2. - С. 33-42. - Бібліогр.: 21 назв. - англ. Індекс рубрикатора НБУВ: К235.17
Рубрики:
Шифр НБУВ: Ж44086 Пошук видання у каталогах НБУВ
|
| | | | |
11. |
Dzyubyk A. Optimization of conditions of electroslag welding of bandings of rotary units / A. Dzyubyk, L. Dzyubyk, Ya. Zinko, S. Biruk // Ukr. j. of mech. eng. and materials science. - 2016. - 2, № 2. - С. 43-52. - Бібліогр.: 14 назв. - англ.The design of banding shells of rotary units is analyzed. It is shown that combined welding and cast manufacturing of bandings is used in the case of large structural sizes. The basic materials (30, 35, 25 HSL and 30 HML), being used in this process, are characterized by the tendency of forming of hardening structures due to the thermal cycle of welding. As a result of this, the cracks in the heat-effected zone, which lead to the destruction of the connection under the influence of welding residual stresses. The analysis of literature sources has shown that the usage of electroslag welding is perspective during the manufacturing and welding of operational cracks. Thus it is important to define the correct parameters of the welding conditions. In the case of electroslag method they are different from the arc methods and are characterized by the larger amount. In the paper the technological process of welding of banding (tread) ring with the external diameter of 4600 mm, wall thickness of 300 mm and wideness of 500 mm, which is made of steel 35. The defining of regime parameters is made using the following recommended techniques: taking into account the chemical composition of the basic metal; according to the nomogram depending on the ratio of the thickness of the metal to the number of electrode wires; using the calculation (design) method according to the conditions of electroslag welding of the banding. Taking into account the tendency of the steel 35 to cracks forming (cracking), the evaluation of the structure and phase composition and mechanical properties of metal of heat-effected zone of the weld. In order to define the microstructure, the cooling rate of the metal in the range of structural transformations was determined and the diagram of anisothermal decomposition of austenite was used. The technique of determination of the metal cooling rate as a result of the influence of thermal cycle of electroslag welding is proposed in the paper. It is based on the usage of special nomograms which characterize the specific features of the process being studied. The cooling rate equals degrees per second when using the developed process parameters. Also the investigation of temperature distribution in the cross-section of the weld has been carried out. It is shown that there are no significant deviations of temperature when using the proposed regime parameters. This influences the reduction of the level of residual stresses along the thickness of the weld. The analysis of the diagram of austenite transformation has shown that the structure of the steel 35 in the initial state is ferrite one with the mixture of pearlite and bainite. As a result of welding carrying out the structure will have a similar composition with slightly larger content of perlite and bainite. It was defined that their content in the heat-effected zone is as follows: 39 % for ferrite, 61 % for the mixture of perlite and bainite. At the same time, the investigated technology of electroslag process ensures the slow heating and cooling of the areas around the weld and obtaining of satisfactory mechanical properties of the metal. Therefore, the combined usage of existent techniques of regime parameters determination is expedient. Also it is necessary to carry out the verification of physical and chemical properties of the metal of heat-effected zone in order to prevent the formation of hardening structures. Індекс рубрикатора НБУВ: К641.510.023.2
Рубрики:
Шифр НБУВ: Ж44086 Пошук видання у каталогах НБУВ
|
| | | | |
12. |
Barandych C. Lathe turning mode optimisation for parts working under conditions of cyclic loading / C. Barandych, S. Vyslouh, V. Antoniuk, O. Tymoshenko, V. Koval // Ukr. j. of mech. eng. and materials science. - 2016. - 2, № 2. - С. 53-60. - Бібліогр.: 19 назв. - англ.This work is devoted to questions of technological cyclic durability maintenance, of the material for parts working under cyclic loading conditions, by lathe processing optimization. The analysis of the impact of the surface layer quality on fatigue characteristics is described for parts operating under cyclic loads. Survey of methods for evaluating cyclic durability is completed, which showed lack of information about the mathematical relation between the cyclic durability of the part's material and technological conditions of its production. A fatigue experimental study was carried out, the results of which allowed to create a mathematical model of cyclic durability of the material from lathe processing mode and tension cycle. The complex objective function that takes into account the dependence of cyclic durability of turning from technological conditions of handling and processing was developed. It is proposed to determine tension cycle for the most unsafe parts of a constructive element with consideration of conditions of service using the finite element method. The mathematical model of lathe processing of parts working under conditions of variable cyclic loads is developed and represented by total complex target function and system of constraints, including set of constrains on: feed, speed, strength and power of cutting, cutting precision, tool life and roughness of the workpiece. In addition, this mathematical model takes into account the actual characteristics of the material and expands its use to other materials of alloyed chromium steel. Submitted multi-criteria task is solved by using the method of sliding clearance. Steel 40Х GOST 4543-71 was used as an example for the proposed mathematical model of the part turning process, part operates under cyclic loading, and best values for feed and cutting speed are calculated. Індекс рубрикатора НБУВ: К632-6
Рубрики:
Шифр НБУВ: Ж44086 Пошук видання у каталогах НБУВ
|
| | | | |
13. |
Stupnytskyy V. Investigation of the influence of machining factors on the workpiece deformation mode in the chip-forming zone by the finite element method / V. Stupnytskyy // Ukr. j. of mech. eng. and materials science. - 2016. - 2, № 2. - С. 61-70. - Бібліогр.: 11 назв. - англ.The results of studies of the impact strength, temperature factors and parameters of cutting tool geometry on the formation of the stress-strain and thermodynamic state of surfaces with different types of engineering materials in the cutting process are described in the article. Analysis of simulation modeling of power, temperature and deformation parameters is the basis for making of forecasting models of influence of the structure and process parameters on the formation of complex operational properties of the product. Індекс рубрикатора НБУВ: К63-1
Рубрики:
Шифр НБУВ: Ж44086 Пошук видання у каталогах НБУВ
|
| | | | |
14. |
Karpenko M. Experimental improvement of the technology of cutting of high-pressure hoses with metal braid on hand cutting machine / M. Karpenko, M. Bogdevicius, O. Prentkovskis // Ukr. j. of mech. eng. and materials science. - 2016. - 2, № 2. - С. 71-78. - Бібліогр.: 13 назв. - англ.In the article the review of the problem of improvement of technology of high pressure hoses cutting on the hand cutting machines is analyzed. Different methods of cutting of high pressure hoses into the billets are overviewed and the quality of edge cuts of hoses is analyzed. The comparison of treatment on automatic cutting machines and on hand cutting machines is carried out. Different experimental techniques of improvement of the quality of edges cutting of high pressure hoses are presented. On the basis of experimental method, a new cutting technology which consists in maximally close fixation of high pressure hoses to the cutting disc is proposed. In the basic design of the hand cutting machine, the only supports are provided, so that the cutting of the edge section of high pressure hoses causes the metal braid loosening. The proposed technology excludes the scrolling and bending of high pressure hoses during cutting, so that the loosening of metal braid is also excluded. In the paper it is shown that the scheme of distribution of cutting forces during the cutting of high pressure hoses is presented and the mathematical model of determination of normal and tangential cutting forces is formed. With a help of tensiometric table the values of components of cutting forces during free and fixed cutting of high pressure hoses were defined and their comparison was performed. As a result of the use of this technology the edges of the cut off high pressure hoses meet the necessary requirements without using of complicated technological processes. Індекс рубрикатора НБУВ: К63-1
Рубрики:
Шифр НБУВ: Ж44086 Пошук видання у каталогах НБУВ
|
| | | | |
15. |
Koruniak P. Ways of improvement of operational efficiency of hopper devices / P. Koruniak, V. Shenbor, V. Korendiy, A. Bezpalov, V. Brusentsov // Ukr. j. of mech. eng. and materials science. - 2016. - 2, № 2. - С. 79-88. - Бібліогр.: 16 назв. - англ.The operation of hopper devices, which are used in industry, civil engineering, agriculture and transport, is analyzed on the article. The external factors, which influence the process of charging, storing and discharging of loose cargo (freights) from hopper tanks, are overviewed. The subject of research of presented paper is the improvement of mechanisms of fracturing of products hangs-up (bridges) in hoppers at the stage of designing and setting up of hopper devices. In order to solve the stated problem the schemes of bridges fracturing and the structures of devices for debarment of products bridging and their uniform outflow from the hopper tank are proposed. The proposed schemes are based on the principles used in development of vibratory machinery with mechanical, cam and electromagnetic vibratory principles of structures forming. stiffness of elastic system and of the necessary forces for performing of technological process of bridges fracturing is presented and the recommendations for choosing of the stiffness of the system of elastic elements are suggested. For the hoppers with spring and electromagnetic blocks of bridges fracturing and of metered (batched) feeding of products the structural diagrams of devices are presented and the recommendations for usage of various modifications of devices are suggested. The influence of parameters of flat spring elements on the efficiency of devices operation is overviewed. The structural diagrams of devices with one-cycle and two-cycle electromagnetic vibration exciters and the modifications of elastic systems are considered. the structural diagram of the production prototype of the hopper feeder is presented. The materials of the article, the proposed structural diagrams, the operation scheme of the hopper feeder and the derived analytical formulas may be used by designers, researchers and technologists while improving of existent and developing of new devices. Індекс рубрикатора НБУВ: К724.17
Рубрики:
Шифр НБУВ: Ж44086 Пошук видання у каталогах НБУВ
|
| | | | |
16. |
Vrublevskyi I. Two-mass vibratory conveyor-manipulator with three-component electromagnetic drive / I. Vrublevskyi // Ukr. j. of mech. eng. and materials science. - 2016. - 2, № 2. - С. 89-98. - Бібліогр.: 12 назв. - англ.Vibratory conveyor with three-component oscillations provides the opportunity to move the piece goods and details for any trajectory on a plane. Phase difference between independent horizontal (longitudinal or transverse) and vertical (normal) oscillations releases elliptical vibration of conveyor in plane perpendicular to the conveyor's track. Elliptical vibrations allow increasing conveying velocity and inclination angle of conveyor's track in comparison with the simplest linear vibrations. Three-component oscillations of the conveyor's track are implemented by independent exciters of oscillations in the direction of conveying (longitudinal oscillations), oscillations in the direction perpendicular to conveying in plane (transverse oscillations) and oscillations in the direction perpendicular to conveying plane (normal oscillations) with phase difference between them. Conveying velocity of details moving upon the track varies with the change of phase difference angle and reaches a maximum with a certain angle, depending on several parameters. When electromagnetic exciters of longitudinal and normal oscillations are turned on, conveying details move in longitudinal direction. When electromagnetic exciters of transverse and normal oscillations are turned on, conveying details move in transverse direction. When electromagnetic exciters of longitudinal and transverse oscillations are turned on, conveying details rotate around their axes. When all three exciters are turned on, conveying details move at any trajectory. The change in the ratio of longitudinal and transverse amplitudes and phase difference angles between them allows changing the trajectory of details moving on conveyor's track, making them not only move forward but rotate as well. That's why such conveyor can be called a manipulator. The resilient system of two-mass vibratory conveyor-manipulator with three-component oscillations should have elastic pliability in three mutually perpendicular directions. It includes four resilient elements; each of them consists of two latticed leaf springs, fixed at the right angle to each other. The working body with conveying track is joined with reactive frame by resilient elements. Electromagnetic drive includes four electromagnetic exciters of longitudinal oscillations, four electromagnetic exciters of transverse oscillations and one electromagnetic exciter of normal oscillations. The bodies of electromagnets are fixed on the reactive frame and their anchors are fixed on the working body of conveyor-manipulator. A block diagram of the electrical control of conveyor-manipulator is referred. A voltage is supplied from two phases of three-phase electricity to the coils of electromagnets through diodes, auto-transformers, switches and phase-shifter. The amplitudes of oscillations are regulated with aid of auto-transformers, phase difference between them and the change of conveying modes are carried by switches and phase-shifter. The oscillating system of vibratory conveyor-manipulator has six degrees of freedom and respectively six frequencies of natural oscillation. The formulas for calculating the vibratory conveyor-manipulator's frequencies of natural oscillation are derived. Vibratory conveyor-manipulator with three-component electromagnetic drive was designed and manufactured. Its research and testing show the possibility of conveying details and piece goods at any trajectory. Індекс рубрикатора НБУВ: О931
Рубрики:
Шифр НБУВ: Ж44086 Пошук видання у каталогах НБУВ
|
| | | | |
17. |
Zalutskyi Yu. Analysis of modern investigations of vibratory processes of wheeled vehicles / Yu. Zalutskyi, O. Zhytenko, I. Kuzio // Ukr. j. of mech. eng. and materials science. - 2016. - 2, № 2. - С. 99-108. - Бібліогр.: 34 назв. - англ.The history and modern tendencies of development of cushioning systems are analyzed in this paper. The development of mathematical modelling as a process is denoted, the methods and means are described and the necessary information of model choosing is presented. It is focused on the development of simulation modelling. The approaches of researchers, recommendations, indexes and specific features of evaluation of motion evenness are described. The works of many scientists are dedicated to analysis of car vibrations, evaluation of motion evenness and vibration-proof features. Many of them are devoted to investigation of vibrations, to optimization of basic design parameters of the cushioning system of cars and to development of new cushioning systems which allow reducing of vibratory overloading of trucks of general purpose. Taking into account the problems of motion evenness from the point of view of vibration of cushioning parts, the works of scientists are based on the linear theory of cushioning and the simplest one-mass car models are considered. It is also established that the drawback of usage of such theory consists in the fact that it is impossible to overview separately the vibrations of cushioning parts, which weight transfers to elastic elements of the suspension, and non-cushioning parts. The overview of scientific works dedicated to investigation of dynamics of wheeled vehicles allows to show the limited possibilities of traditional passive suspension system according to continuously increasing requirements to modern structures and to substantiate the necessity of usage of controlled cushioning systems. Among the existing variants of controlled cushioning systems, the half-controlled systems, which are the most optimal from the point of view of motion evenness increasing, energy consumption, complexity of structural implementation and usage safety, are of the greatest interest nowadays. On the basis of analyzed materials, it may be concluded that there exists a great amount of scientific investigations in the field of motor vehicles vibrations many of which are devoted to improvement of vibration-proof features of cars. Also a number of works are dedicated to investigation of vibratory overloading of industrial, construction and agricultural motor vehicles which are engaged in transportation of cargo of general purpose. However, too small attention is payed to development of techniques of determination of design parameters of cushioning systems of trucks which are engaged in transportation of cargo of special purpose, for example, cars transportation, where essentially greater attention should be payed to vibratory loadings which act upon such cargo during uneven motion. Індекс рубрикатора НБУВ: О12-01
Рубрики:
Шифр НБУВ: Ж44086 Пошук видання у каталогах НБУВ
|
| | | | |
18. |
Pogrebnyak A. Hydrocutting of frozen food products / A. Pogrebnyak, V. Pogrebnyak // Ukr. j. of mech. eng. and materials science. - 2017. - 3, № 1. - С. 1-8. - Бібліогр.: 10 назв. - англ.The article aims to determine the peculiarities of macromolecule deformation behavior under conditions of a jet-shaping head that would allow to solve the issue related to the mechanism of increasing water-jet cutting power with polymer additions. The roles of longitudinal and transverse velocity gradients in the manifestation of distinctive features of polymer solution flows are analysed. In converging polyethyleneoxide solution flow macromolecules are forced by a hydrodynamic field to rather strong stretching that causes the dynamic structure formation in solutions. There have been studied experimentally velocity fields and their gradients as well as the degree of macromolecule unrolling under pattern conditions of a jet-shaping head in polyethyleneoxide solutions flow. In converging polymer solution flow macromolecules are forced by a hydrodynamic field to rather strong (~ 60 % and more) stretching that causes the field restructuring. The determined regularities of macromolecules behavior in the flow under conditions of a jet-shaping head and manifested in this case effects of elastic deformations have paramount importance in understanding the mechanism of "anomalously" high cutting power of water-polymer jet. The work for the first time makes it possible to explain the nature of increased water-jet cutting power with polymer additions when cutting food products. Understanding the nature of increased cutting power of water-polymer jet will make it possible to develop recommendations on choosing regimes for water-polymer jet processing of food products by cutting. Індекс рубрикатора НБУВ: Л812.14
Рубрики:
Шифр НБУВ: Ж44086 Пошук видання у каталогах НБУВ
|
| | | | |
19. |
Andrusyk Y. Propagation of plane elastic-tough-plastic waves in the material with yield delay / Y. Andrusyk // Ukr. j. of mech. eng. and materials science. - 2017. - 3, № 1. - С. 9-26. - Бібліогр.: 18 назв. - англ.The use of electromechanical model of ideal elastic-tough-plastic material with yield delay while investigating the propagation of plane one-dimensional waves is being considered. The materials being investigated possesses the property of toughness only in the plastic region and is elastic up to the plastic state. The solving of the problem is being carried out in the conditions of one-parameter loading when the permanent (steady) uniformly distributed stress is being suddenly applied to the boundary surface of non-deformed half-space. The value of applied stress exceeds the limit level of elastic state in the case of static deformation and remains unchanged for the whole region of disturbed half-space. In order to conduct the corresponding calculation the dependence between the components the tensor of normal stress and linear deformations along the load axis is being determined. The defining equations of elastic-tough-plastic medium behind the front of the wave of transition from elastic to plastic state are being derived and the simple relationship for determination of the time (duration) of yield delay is deduced. The basic solution of these equations is obtained for the stresses in elastic and plastic region of the half-space. The special representation of the basic pattern of changing of lateral (transverse) stresses and longitudinal deformations for the region of active loading of material is defined. The distribution of velocities of the half-space points in the plastic region is obtained. The difference between the characters of propagation of plane elastic-plastic wave and the wave processes in the material with yield delay is shown. It is noted that two different solutions are obtained despite of the simple type of loading. The first one detects the strange character of medium&s behaviour when the material of disturbed halfspace in the plastic region is in the state of "trembling", which causes the pulsations of lateral (transverse) stresses and the impulses of deformations along the axis that is normal to the boundary surface of the half-space. Індекс рубрикатора НБУВ: В251.203.5
Рубрики:
Шифр НБУВ: Ж44086 Пошук видання у каталогах НБУВ
|
| | | | |
20. |
Biloborodchenko V. Applied model of assessment of intensity of the stressed deformed state of pipelines by evaluation of magnetic anisotropy of coercive forces. Pt. 1 / V. Biloborodchenko // Ukr. j. of mech. eng. and materials science. - 2017. - 3, № 1. - С. 27-36. - Бібліогр.: 7 назв. - англ. Індекс рубрикатора НБУВ: К222.234.77 + Ж820.5 с
Рубрики:
Шифр НБУВ: Ж44086 Пошук видання у каталогах НБУВ
| | |
|
|